Work Hours
Monday to Friday: 7AM - 7PM
Weekend: 10AM - 5PM
Inventory Management App (Onsite): Avoid Delays & Over Ordering
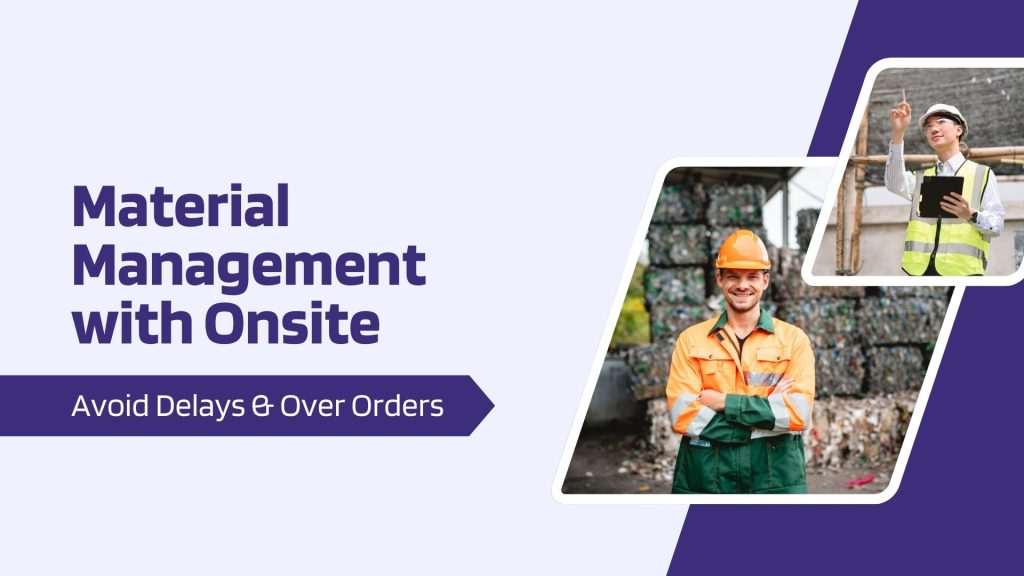
As the construction industry grows, many still struggle with material delays, over ordering, and poor record-keeping, mainly due to outdated, manual processes. Real-time control is essential, yet many contractors remain unaware of smarter solutions. If you’re facing these challenges, Onsite is the answer. It helps you manage material requests, track deliveries, avoid duplicate orders, and maintain clear records, all in one place. Looking for an inventory management app? Switch to Onsite. Let’s see how this works.
Onsite: Inventory Management App to simplify Material Management
1. Material Library
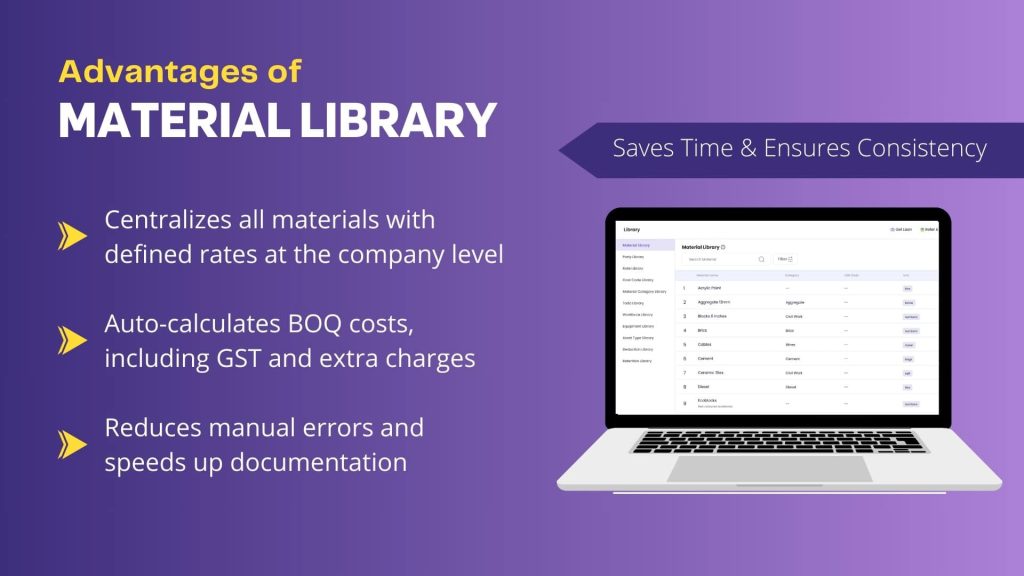
With Onsite, you can make a material library on the company level and state their rates. So, whenever you want to make a BOQ, your rates will be automatically calculated based on the material library. You can make changes accordingly if you want to. From GST to extra charges, anything can be defined in your BOQ. Adding material to the material library also makes it easier to add stock transactions in your projects.
2. Material Request
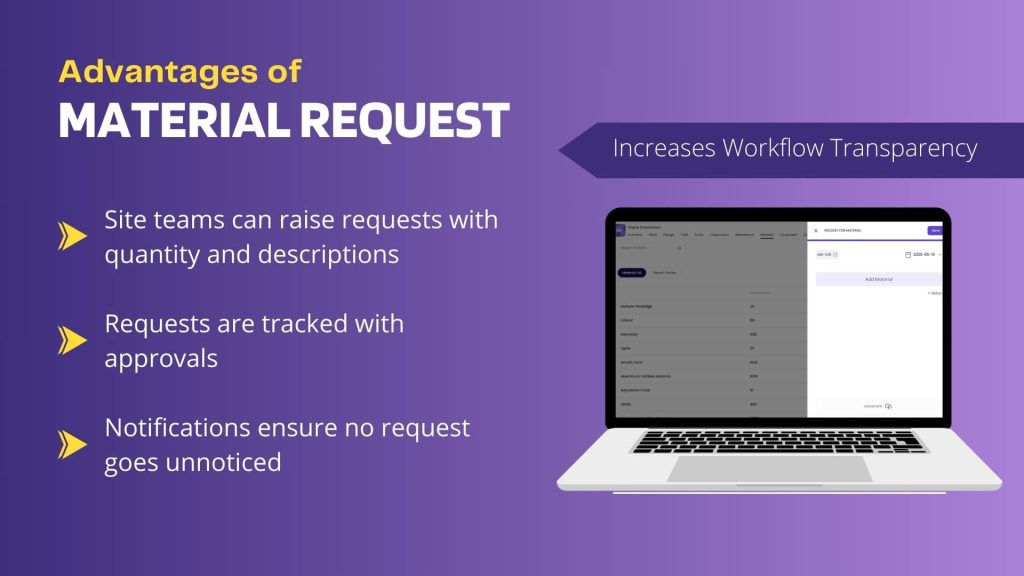
In our Inventory Management App, material management is easier as every step is organized. A site manager or supervisor can simply make a material request. He can describe what material is needed and how much its quantity is needed. This request can be seen in a material, and you can also get a notification of it. In this way, it’ll be clear on what date how much material was requested. When a material is requested, it is up to the contractor or owner whether to approve this request or not. Once approved or rejected, this activity can be seen by the person who is responsible for making purchases.
3. Material Purchase
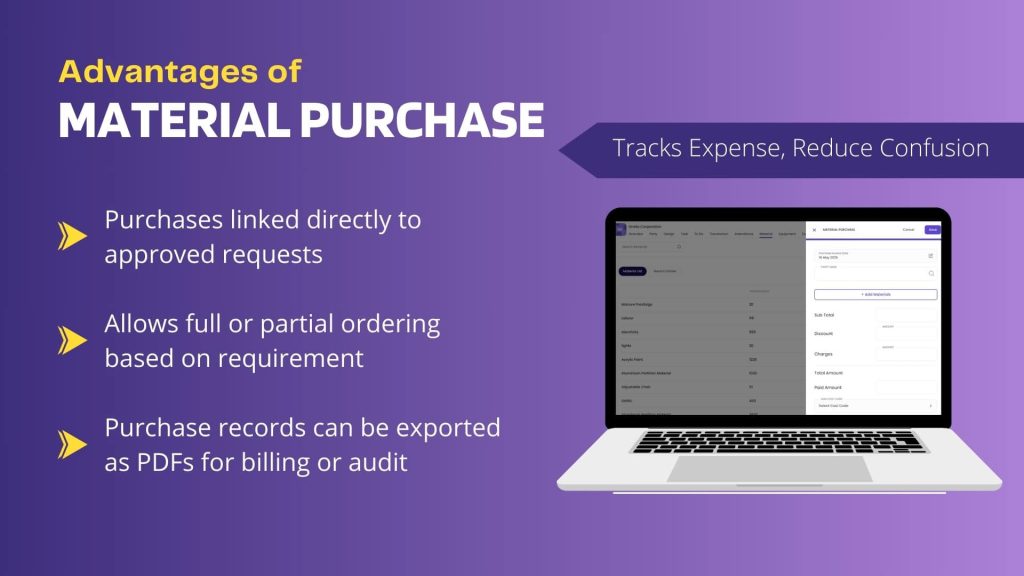
Once the material is approved, a purchase will be made by the backhand team. While making a material purchase, you can state if the full amount is being ordered or is it done partially. This purchase transaction will be recorded in the software, and you can even generate a report of it in a PDF form.
4. Procurement
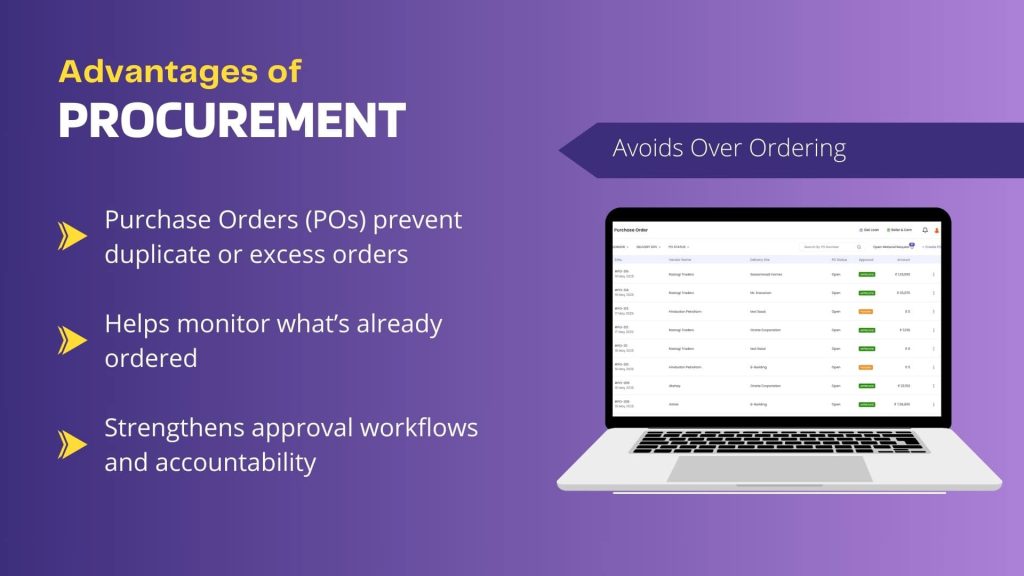
From the procurement section, your backhand team can generate a purchase order. With the help of an PO, you can avoid over ordering By tracking what’s already been ordered through POs, you avoid placing duplicate or excess orders, saving both money and storage space. It also helps in streamlining approvals and accountability. Also POs are essential for audits, billing, and verifying that orders were delivered as agreed.
5. Material Received and Material Used

Once the purchase is made, it is also necessary to track if the material has been received at the site and if yes, how much of it was delivered. This also can be tracked within the app. Once the material received traction is being made, the Site supervisor can also define how much of this material was used. You can even track the used material on an every day basis.
6. Material Transfer
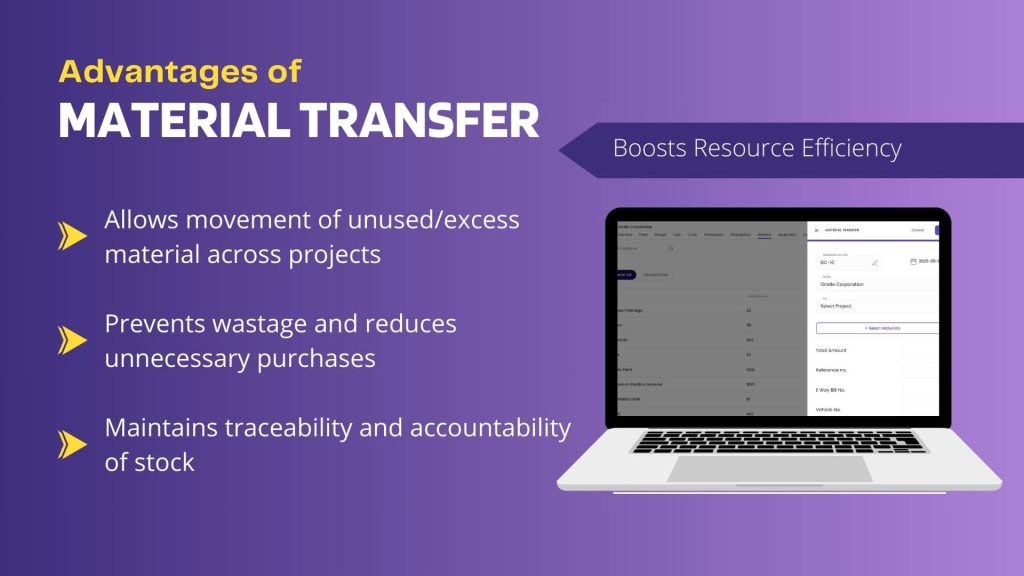
Often, if mistakenly over-ordered material is saved it can be transferred to the other projects or can be returned. With this feature, you can make a material transfer, and it can be recorded within the app. So that there will be no loss of material, better resource utilization, and complete traceability across all your sites. This ensures nothing goes to waste and every material movement is accounted for.
Conclusion
If you are someone who is looking for an Inventory Management App that helps in better material management then this article is for you. Onsite is a construction management software made for streamlining multiple projects. You can have access to your projects anytime and anywhere. Multiple construction business owners trust us. We not only help in providing an Inventory Management App but we make your construction business easier than it can ever be.
Also Read: Reducing Manual Errors in Payroll Management System with Onsite Software
FAQs
1. What is Onsite and how does it help with material management?
Onsite is a construction management software that helps contractors streamline material management by enabling material requests, tracking usage, managing transfers, and preventing over ordering.
2. How does the material library in Onsite benefit contractors?
The material library allows you to maintain a centralized list of materials with predefined rates. This helps auto-calculate BOQs, maintain consistency, and simplify stock transactions.
3. Can I track material usage and deliveries in Onsite?
Yes, Onsite allows you to track material received at site and monitor daily usage. This helps reduce wastage and ensures accurate reporting of inventory.
5. How does Onsite prevent over ordering of materials?
With purchase orders and approval flows in place, Onsite lets you see what’s already been ordered. This avoids duplicate purchases and saves money.
5. Is it possible to transfer unused materials between projects in Onsite?
Absolutely. Onsite allows material transfers across projects, ensuring better resource utilization and reducing material waste.