Work Hours
Monday to Friday: 7AM - 7PM
Weekend: 10AM - 5PM
Brick Manufacturing Process: Insights Into The Production & Quality Control
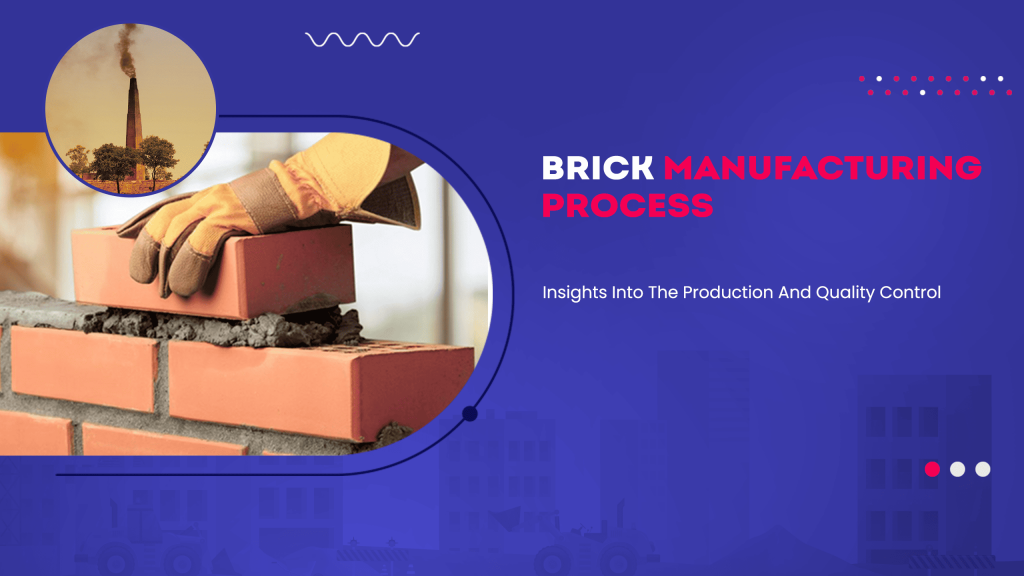
Bricks are highly energy-efficient, sustainable building materials that require minimal maintenance. They have been used as building materials for a long period of time. Meanwhile, the brick manufacturing process remained unchanged except for the measures taken to enhance their quality. Bharat Brick Pvt. Ltd, Sri Ventakeshwar Bricks, and Fly Ash Bricks are some enterprises known for high-quality brick manufacturing in India. Let’s have a look at the brick manufacturing process and the factors that govern their quality.
Free Brick Calculator: Free Brick Calculator for Wall | Estimate Bricks Requirement
Brick Manufacturing Process
Clay is the main ingredient in the manufacturing of bricks. The different steps involved in the manufacturing process are as follows.
1- Preparation Of Clay
The first and foremost step in the brick manufacturing process is the preparation of clay. In this process, the purest form of clay is obtained from the grounds for further processing. It is a step-by-step process and is carried out as follows.
- Unsoiling of clay: In this step, the top layer of the soil is removed for up to 200 mm. The top layer contains coarse particles and impurities such as vegetative matter, stones, pebbles etc that are unfit for an ideal clay. This process is called Unsoiling.
- Digging: After removing the top layer, the clay is dug out and spread on uniform ground.
- Cleaning: The clay is then looked for any remaining impurities, gravel, coarse sand, etc. Any clay lumps, if present, are dissolved and the final clay is obtained in fine powder form.
- Weathering: In this process, the clay is exposed to weather conditions for 3-4 weeks. It is carried out in the rainy season. Weathering is done to obtain soft and homogenous clay.
- Blending: In this step, the clay is mixed with other ingredients like fly ash, sandy loam, and calcareous earth and blended with water. Blending helps in improving the quality of clay.
- Tempering: After blending the clay with additives and water, it is kneaded either manually or through brick manufacturing machines called pug mills. This process gives a homogeneously mixed clay with improved plasticity. The clay is now ready to be moulded.
2- Moulding Of Clay
In this step, the prepared clay is moulded into any desired shape. However, the bricks used for the construction are rectangular and are 19 cm X 9 cm X 9 cm. The tempered clay mix is poured into rectangular moulds. Moulding is done in two ways:
- Hand moulding
It is done in small-scale manufacturing of bricks. There are steel or wooden moulds in which tempered clay is poured. - Machine moulding
For large-scale manufacturing, the clay is moulded through brick manufacturing machines intended for moulding. It is a more precise method and bricks obtained through this process are high in strength.
3- Drying Of Bricks
Once the bricks are removed from the mould, they are arranged in proper rows and hacks under a shed for natural drying. However, if the bricks are manufactured on a large scale, artificial dryers are used. This process can take up to 4-8 days. It is a critical stage and th bricks must be handled with care to maintain their strength while drying.
4- Burning Of Bricks
When the bricks are dried up to 85-90% they are burnt in kiln to attain their physical properties. The burning is done at a temperature of 800-1100°C. Burning is either done in an open clamp furnace or kiln. It takes up to two weeks to complete the burning process. After burning the brick attains its full strength and is ready for packaging and supply.
Also Read: Best Types of Bricks Used by Top Contractors For House Construction
Factors Governing The Quality Of Bricks
- Clay Conditioners: Adding clay conditioners in the process of mixing and blending gives a homogenous mix and improves the strength of the bricks.
- Blending and tempering: A well-blended mix improves the quality of bricks by many folds. The ingredients added to the clay while blending helps in improving the strength. Tempering done through pug mills is more efficient and gives higher-quality bricks than manual tempering.
- Burning temperature: The burning temperature in the kiln directly affects the strength of the bricks. Burning the bricks at a lower temperature would not impart the required strength. A temperature higher than 1300℃ would make the bricks brittle and easily breakable.
- Proper Handling: Care should be taken while drying, cooling, stacking and loading-unloading bricks to avoid any physical damage that may hamper the strength.
- Fuel in the kiln: The quality of bricks also depends on the type of fuel used while burning. Continuous kiln provides the most effective heating to the bricks and thus improves their strength.
Conclusion
For laying a strong foundation and enhancing the quality of infrastructure, it is mandatory to use high-quality bricks. This article will give you a strong insight into the brick manufacturing process and factors affecting the quality of bricks and help you choose the best building material for your construction project.
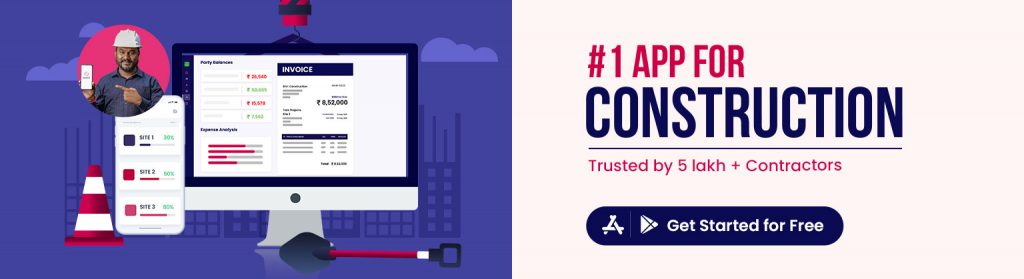
People also search for: unsoiling of bricks, insights bricks, brick manufacturing process, manufacturing process of bricks, brick production process, unsoiling, red brick manufacturing process, bricks manufacturing process,