Work Hours
Monday to Friday: 7AM - 7PM
Weekend: 10AM - 5PM
How to Streamline Material Inventory Management Without WhatsApp but with Onsite
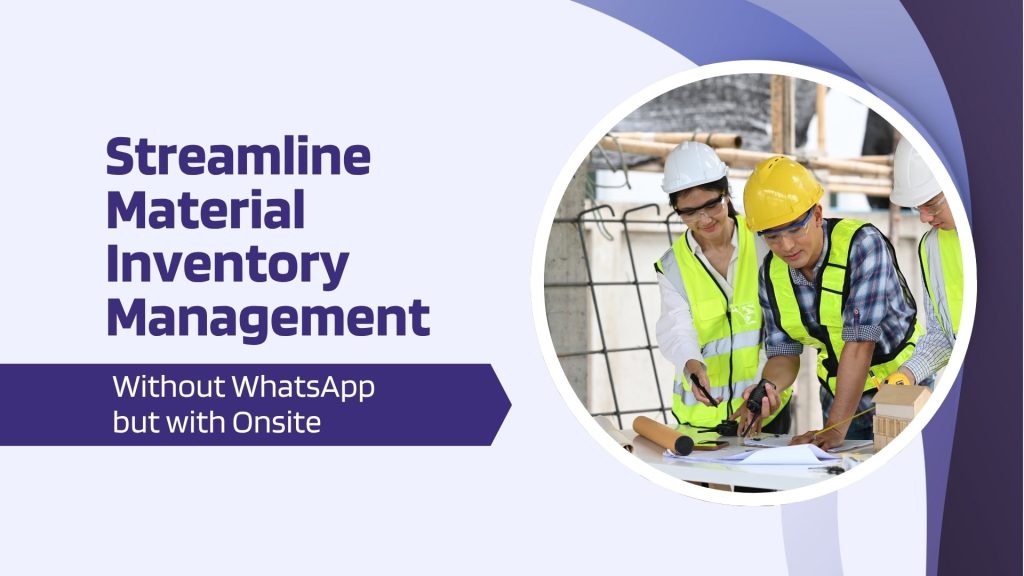
As the construction industry grows, many still struggle with misunderstandings, frequent material shortages, and a complete lack of visibility on stocks mainly due to outdated, manual processes. Real-time control is essential, yet many contractors remain unaware of smarter solutions. If you’re facing these challenges, Onsite is the answer. You do not have to rely on WhatsApp and Paper Logs. Onsite helps you manage material requests, track deliveries, avoid duplicate orders, and maintain clear records, all in one place. Looking for a better way to handle Material Inventory Management? Switch to Onsite. Let’s see how this works.
How Onsite Helps You Streamline Material Inventory Management
1. Track Site Inventory in Real Time
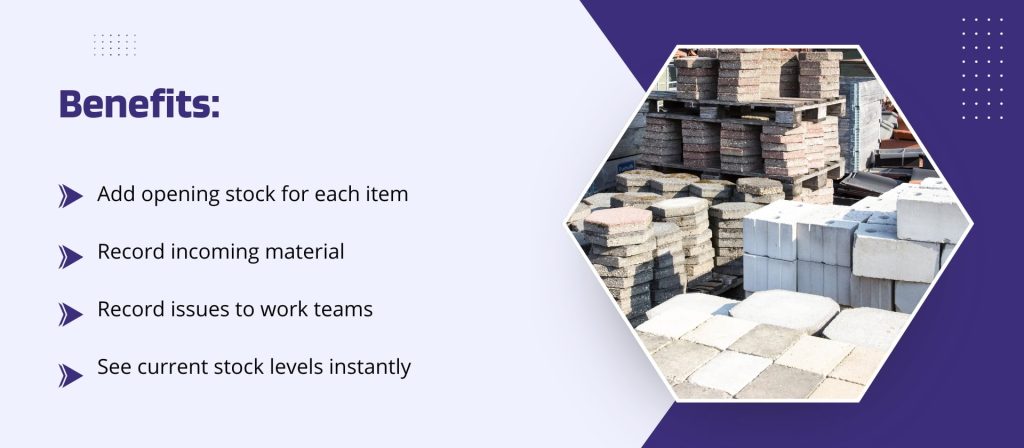
When subcontractors at site use materials, they can just update the amount of material that has been used at the site. In this way you can know how much material has been used or how much is remaining at the site. This helps in streamlining your material inventory management.
2. Reduce Material Wastage and Over-Ordering
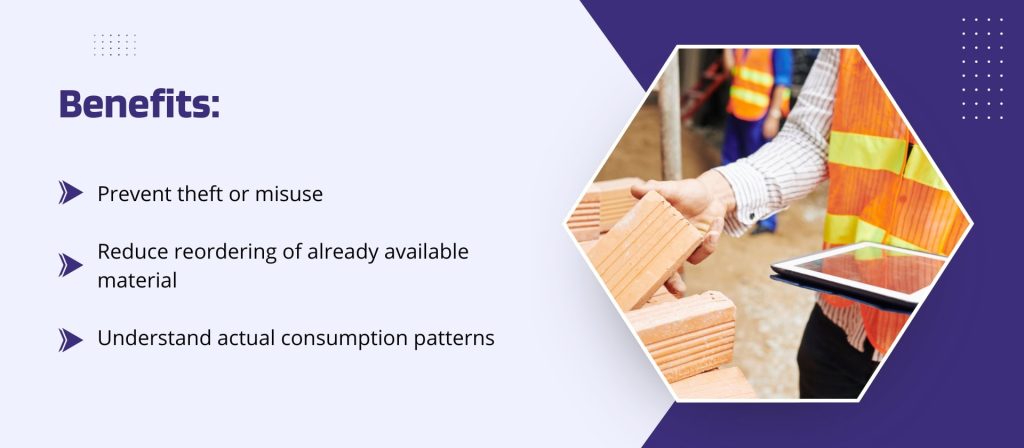
By real-time updates, you can get to know how much material is needed at a site and by knowing the accurate material requirement you can avoid ordering extra material which helps in avoiding the material wastage. If the material wastage is controlled, you are also getting benefits of cost saving.
Onsite is specially made for construction sites. With this streamlined material inventory management, a site supervisor can make a material request from the site, which is approved by a management team, which later on can lead to making material purchase. This material purchase will reach the site, and you can also keep track of how much of it has been used. With this software, you can track how much of the material is being used every day. If not used, you can also make an entry of material transfer to the other site. Every activity related to material can be tracked here. With our app, within three months, you can see a 20% drop in excess inventory. Teams will stop over-ordering because they could see what was already available. The savings will be immediate and impactful.
3. Better Coordination Between Site & Backhand Team
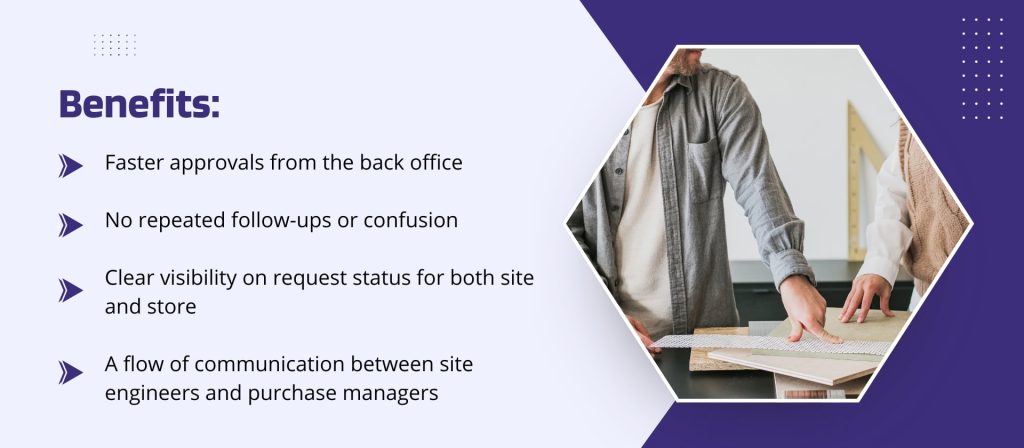
Whenever your site team needs material at site, they can just make a request through our software and not from WhatsApp because there are often chances that requests can go unnoticed which can lead to delay in work. But with Onsite, nothing goes unnoticed. Every material request is automatically notified to the concerned person and tracked until fulfilled. This creates a smooth flow between site engineers, store in-charges, and the backhand purchase team. Everyone stays updated on the status of each request, which removes confusion, avoids duplication, and ensures materials reach the site on time. This kind of real-time coordination keeps your projects moving without miscommunications.
4. Reports That Actually Help You Make Decisions
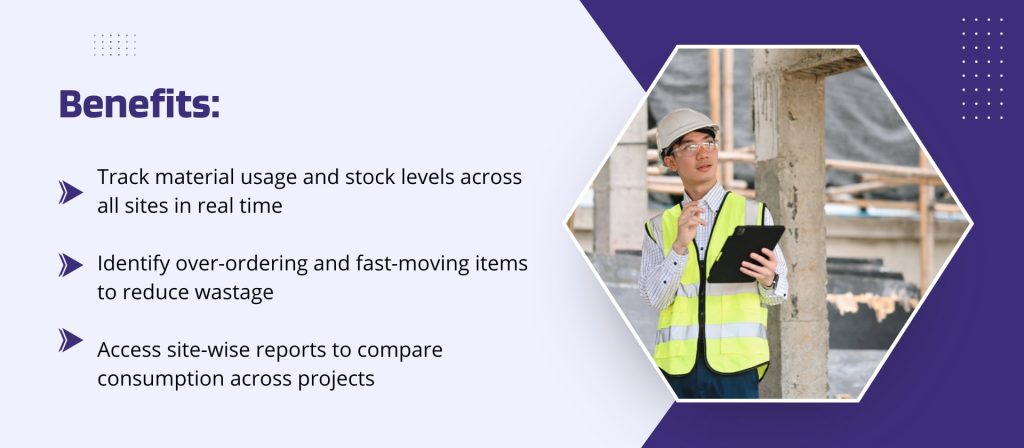
With data available in your digital tool, you can immediately generate reports and get to know how much of each material has been used over a time period and which sites are consuming more (or less) than expected. You can also get to know if there is any over-ordering at a site. Without any lost reports on WhatsApp, you can actually access and generate reports from Onsite, that helps you make better decisions.
Conclusion
If you are someone who is looking to streamline their material inventory management that helps in better material management then this article is for you. Onsite is a construction management software made for streamlining multiple projects. You can have access to your projects anytime and anywhere. You do not need outdated ways like WhatsApp and Spreadsheets. Multiple construction business owners trust us. We not only help in providing an Inventory Management App, but we make your construction business easier than it can ever be.
Also Read: Construction Digital Workforce Management Importance & How Onsite Helps?
FAQs
1. Why should I stop using WhatsApp for inventory management?
WhatsApp is not built for structured tracking. Important material requests can get buried in chats, approvals are often missed, and there’s no real record of usage or stock. Onsite provides a proper system where every material request, approval, usage, and transfer is tracked in real time, reducing errors and delays.
2. How does Onsite help track material inventory in real-time?
With Onsite, your team can update material usage directly from the site. You’ll always know how much material is available, how much is used, and when more is needed, across all your projects.
3. Can Onsite help me avoid over-ordering of materials?
Yes. When you know exactly how much material is in stock, you’re less likely to order more than needed. Onsite also alerts you when a requested material is already available, preventing duplicate orders and saving cost.
4. Who in my team can use Onsite for inventory tracking?
Anyone involved in site execution and material handling, including site engineers, supervisors, store in-charges, and purchase managers, can use Onsite. The system ensures everyone is aligned, and all actions are recorded.
5. How does Onsite improve coordination between the site and the purchase team?
Material requests raised from the site are instantly visible to the backhand team. They receive alerts, can approve requests digitally, and track their fulfillment status- reducing the need for repeated follow-ups and miscommunication.