Work Hours
Monday to Friday: 7AM - 7PM
Weekend: 10AM - 5PM
Inventory Management in Construction: Unique Challenges
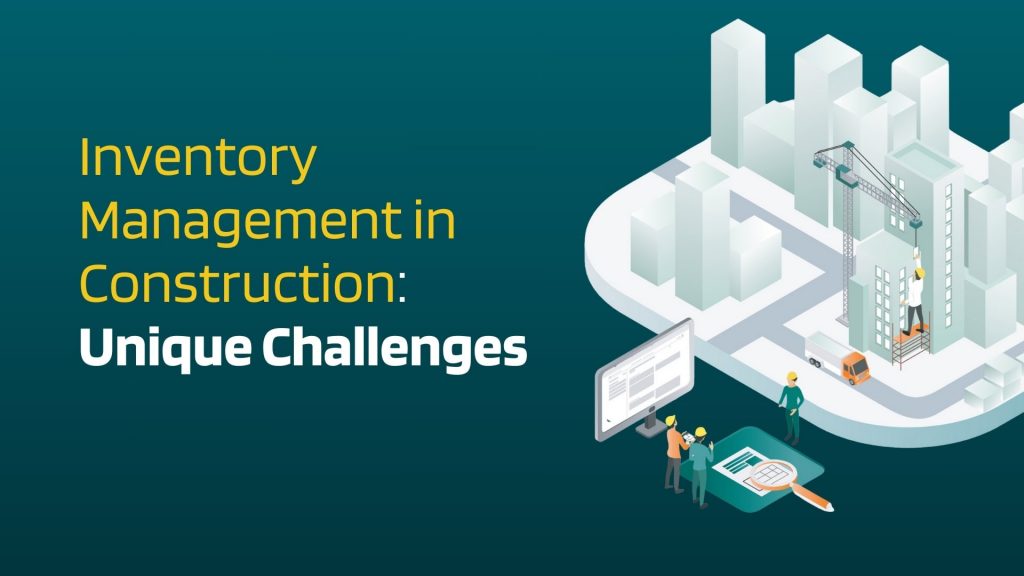
Inventory plays a necessary role in the construction industry. Keeping its track and managing its pricing is a must otherwise your project’s budget and planning will be shaken. There are often times when the materials cost too much, sometimes it’s overstocked, sometimes there’s shortage, and just like this there are many factors that affect the management of inventory in construction. Let’s get to know about unique challenges that are faced during inventory management.
Inventory Management Challenges & their Solutions
1. Decentralized Inventory Locations
Unlike other industries, construction companies store their inventory at different locations. It is not limited to warehouses. This causes many complications in managing and tracking of inventory which is why it is necessary to have an organized tracking system of every site and material available there. This problem can be solved if you digitize your inventory management. Onsite is a tool that helps to keep track of inventory with the help of which you can save cost and avoid material wastage too.
2. Material Variability
Inventory management can be complex as there are many varieties of material that is used at a construction site. From bulk materials to a small pack of nails, material management demands detailed tracking. Traditionally, people used to track inventory by counting them but now the industry has digitized. Now you can keep count of material and update its usage within the construction management software like Onsite.
3. Cost Control
Often in case of overstock and shortage of material, cost affects a lot. You make a budget, but the inventory expense never stays in budget. Keeping a project under budget is the topmost priority of a lot of contractors or builders. Cost control in inventory management requires visibility into the financial aspects of procurement and usage. So, construction management software helps in tracking and monitoring of material which helps in updating exactly where the material has been used and placed. It helps in proper utilization and cost control.
4. Material Wastage
In case of wrong assumption of usage and overstocking, material gets wasted which also affects the cost saving of the project. Poor planning, and incorrect orders are often the cause of material wastage. With the help of Onsite, you can avoid material wastage by better planning and tracking of material. Make accurate purchase orders, estimate usage, keep track of material, and get real-time updates with Onsite.
5. Supplier Coordination
It is necessary to make good coordination with suppliers as their actions can affect a construction project on a major level. Delay in supply of inventory and incorrect material delivery can lead to trouble and project delays. It is necessary that a clear communication and understanding is made with suppliers so that dispute and trouble can be avoided. Construction software like Onsite that includes supply chain management features can streamline communication and provide real-time updates on order statuses. This way, contractors can adjust plans based on supplier availability, minimizing delays.
Conclusion
So, if you are someone who is having trouble in inventory management and often face problems like PO generation, bill generation, poor planning, material wastage, material tracking, etc then you can switch from traditional ways to digitized way. With inventory management software, you can keep track of your inventory and manage them efficiently. If you are looking for such tools, then Onsite is one of the best tools out there that can make your inventory management efficient.
Also Read: Top 5 Workforce Management Tools to Optimize Your Construction Projects
FAQs
1. Why is inventory management important in the construction industry?
Proper inventory management ensures that materials are available when needed, helping to prevent costly delays and avoidable expenses. Mismanaged inventory can lead to material shortages, overstocking, budget overruns, and disrupted project timelines.
2. What challenges arise from decentralized inventory locations in construction?
Construction materials are often stored across multiple locations, including job sites, warehouses, and supplier facilities, which can make it challenging to track and manage inventory efficiently. Using a digital solution like Onsite can provide real-time visibility into material levels across all locations, improving control and reducing errors.
3. How does material variability affect inventory management in construction?
Construction projects involve a wide range of materials, from bulk items to small components, making tracking and managing inventory complex. Modern solutions, like Onsite, streamline the process by digitizing inventory tracking, allowing contractors to monitor the status and availability of various materials with ease.
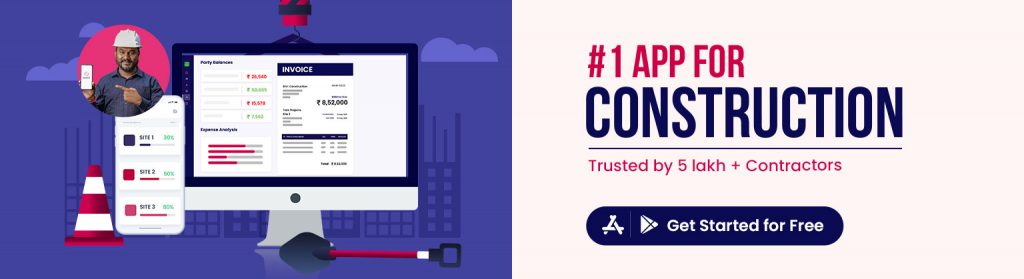