Work Hours
Monday to Friday: 7AM - 7PM
Weekend: 10AM - 5PM
8 Important Soil Tests for Construction
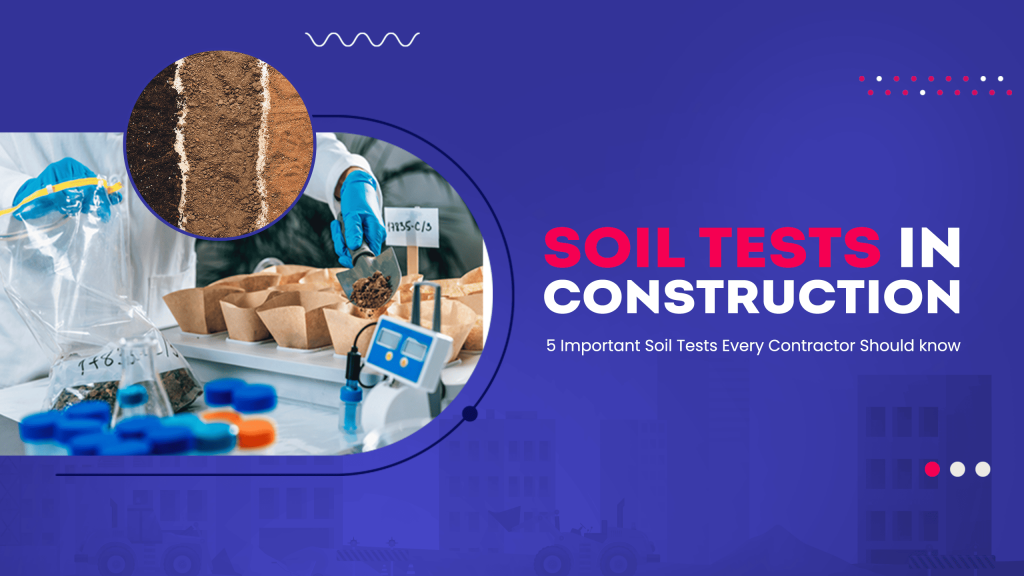
Soil testing refers to analyzing the soil’s physical, mechanical, and chemical properties before commencing the construction work. Soil tests in construction is essential to ensure the quality of your building structures. It gives a brief idea about the bearing capacity of the soil. There are various soil testing procedures carried out to determine the different parameters of soil. Some of the soil testing methods in construction are listed below.
Why Soil Tests for construction is Important?
Soil testing holds great significance in the construction industry, making it essential for every contractor to possess knowledge about this crucial process. Understanding the properties and characteristics of soil at a construction site is vital to ensure the structural integrity, stability, and safety of any building or infrastructure project.
First and foremost, contractors benefit from identifying the soil type present on the site. Different soil types, such as clay, silt, sand, or their combinations, exhibit varying load-bearing capacities and behaviors when subjected to external forces. Knowing the soil type empowers contractors to make informed decisions regarding design and foundation requirements, ensuring the structure can withstand anticipated loads and environmental conditions.
Additionally, soil testing provides valuable insights into soil compaction and moisture content. Adequate compaction is vital in preventing settling, differential settlement, or soil instability that can lead to structural damage and safety hazards. By conducting soil tests, contractors can determine the optimum level of compaction and moisture required for a stable foundation, enabling them to adapt their construction methods accordingly.
Furthermore, soil testing allows contractors to identify potential issues such as expansive soils, high water tables, or soil contamination. Expansive soils can cause significant foundation movement due to moisture fluctuations, resulting in cracks and structural damage. High water tables can impede proper drainage and compromise structural stability. Soil contamination poses environmental risks and can impact the long-term durability of the construction. By conducting soil tests, contractors can mitigate these risks through appropriate measures and modifications to the design and construction process.
Moreover, understanding the bearing capacity of the soil is critical in determining the size and depth of foundations. Soil tests provide valuable data on the load-bearing capacity, enabling contractors to design foundations that effectively distribute the weight of the structure. This ensures the foundation can support the intended loads and prevent settlement or structural failure.
Popular Methods of Soil Tests for Construction
Different soil parameters are tested before construction, such as its chemical composition, density, specific gravity, and load-bearing capacity. The various types of soil testing in construction are as follows.
1- Dry Density Test
It is done to determine the density of soil particles per unit volume of soil excluding the moisture content. The dry density test is carried out in two ways:
a) Core Cutter Method
In the core cutter method, a cylindrical cutter is used of specific dimensions. The core cutter is inserted into the soil and a portion of the soil is extracted and weighed. The water content of the soil is determined, and the density of the soil is calculated through the following formula – P = (M / V) / 1+ W
b) Sand Replacement Method
In this method, a portion of soil is excavated from the earth using a metallic sieve for calculating its dry density. This soil is dug by creating a circular hole in the earth. The hole is replaced by sand of known density. The volume of the hole is calculated to find the dry density of the soil.
2- Moisture Test
This test is conducted to determine the moisture content of the soil on which the foundation has to be laid. Different methods used for moisture testing are oven drying method, calcium carbide, radiation method, sand bath method, and alcohol method.
3- Atterberg Limits Test
The Atterberg limits test is performed to determine the liquid limit, plastic limit, and plasticity index of the soil. The liquid limit test is done to determine the moisture content and consistency of the soil at which it acts more like a viscous liquid rather than a plastic clay. A Casagrande device is used to measure the liquid limit of soil.
The plastic limit of the soil determines the limit at which the soil acts as a brittle solid. In this soil testing procedure, the soil is mixed with water and spread on a glass sheet. Slowly a cylindrical roll of soil is made with hand until the roll breaks and crumbles. When the soil crumbles at 3 mm diameter, the water content of the soil is noted to determine its plastic limit. The plasticity index of the soil is calculated by subtracting the plastic limit from the liquid limit.
4- Specific Gravity Test
The specific gravity of the soil is calculated as the ratio of the soil density to the density of water. The density bottle method, pycnometer method, gas jar method, and shrinkage limit method are various ways to determine the specific gravity. This soil testing procedure determines the vulnerability of soil corrosion and its susceptibility to float away with floods.
5- Soil Tests for Construction
This test is carried out to find the compaction of the soil. It reduces the air voids to densify the soil.
Proctor’s compaction test is a widely utilized laboratory test in the construction field to determine the optimal moisture content and maximum dry density of soil. This test enables engineers and contractors to evaluate the compatibility and compaction characteristics of soil, specifically for designing and constructing earthwork projects like embankments, roads, and foundations.
The Proctor’s compaction test follows a standardized procedure outlined in various national and international standards, such as ASTM and IS codes. The test involves compacting a representative soil sample in a compaction mold under controlled conditions of moisture content and compaction effort.
Step 1:
The first step of the test involves obtaining a representative soil sample from the site. The sample is then dried, crushed, and sieved to eliminate coarse particles or organic materials. The resulting soil sample is divided into different moisture content increments.
Step 2:
Next, the compaction mold, typically in a cylindrical shape, is filled with the moist soil sample in layers. Each layer undergoes compaction using a specified number of blows from a compaction hammer or a mechanical compactor. The compaction effort typically relies on the weight of the compaction hammer and the fall height. This process is repeated for each moisture content increment.
Step 3:
Following compaction, the compacted soil specimen is carefully extracted from the mold and weighed to determine its mass. The moisture content of the specimen is determined by drying it in an oven and comparing the initial and final weights. The dry density of the specimen is calculated by dividing its mass by the volume of the mold.
The test is conducted for various moisture content increments, spanning from dry to wet conditions. The moisture content versus dry density data is plotted on a compaction curve, commonly known as the Proctor curve. The maximum dry density and corresponding optimum moisture content can be derived from this curve.
The results of the Proctor’s compaction test furnish crucial information for the design and construction of earthwork projects. The maximum dry density represents the highest achievable density for a given soil under specific compaction conditions. The optimum moisture content signifies the moisture level at which the soil can be most effectively compacted, resulting in the highest density.
Engineers and contractors utilize the results of the Proctor’s compaction test to determine the necessary compaction effort and moisture control during construction. This aids in optimizing the compaction process, ensuring stable and durable structures by achieving the desired density and minimizing the risk of settlement or soil-related issues.
6- California Bearing Ratio Test
The purpose to of California Bearing Ratio is to test the strength of the soil. It is basically done when to see if the soil can support road and pavement construction. It helps in providing the information about the strength of the soil. The method of this test is done by a plunger which is pressed into the soil sample and then its resistance is compared of the standard value.
7- Permeability Test
Permeability Test is the test to measure the rate at which water can flow through the soil. It is helped in the designing of drainage systems and predicting the risk of the soil erosion.
8- Soil pH Test
This test is to measure the pH level of the soil like its acidity or alkalinity. It assures the chemical stability of the soil, and it helps in knowing the potential of corrosion of underground structure.
Also Read: Brick Maintenance and Preservation
Conclusion
In conclusion, it is crucial for individuals involved in agriculture, construction, or environmental science to have a solid understanding of the various soil testing methods. It is important to note that each method serves a specific purpose and should be used in conjunction with others for a comprehensive assessment. By employing these soil testing methods, we have the ability to optimize crop productivity, enhance construction projects, and preserve the environment for future generations.
FAQs
1. How does soil testing help?
By conducting soil tests, contractors can determine the optimum level of compaction and moisture required for a stable foundation, enabling them to adapt their construction methods accordingly. Also, soil testing allows contractors to identify potential issues such as expansive soils, high water tables, or soil contamination. Expansive soils can cause significant foundation movement due to moisture fluctuations, resulting in cracks and structural damage.
2. What is Atterberg limits test?
The Atterberg limits test is performed to determine the liquid limit, plastic limit, and plasticity index of the soil. The liquid limit test is done to determine the moisture content and consistency of the soil at which it acts more like a viscous liquid rather than a plastic clay. A Casagrande device is used to measure the liquid limit of soil.
3. What is Proctor’s compaction test?
Proctor’s compaction test is a widely utilized laboratory test in the construction field to determine the optimal moisture content and maximum dry density of soil. This test enables engineers and contractors to evaluate the compatibility and compaction characteristics of soil, specifically for designing and constructing earthwork projects like embankments, roads, and foundations.
People Also Search For:
soil testing for construction, soil testing methods, soil testing methods for construction, test on soil, soil testing in construction, soil tests, soil tests in civil engineering, soil test in construction, how many types of soil test, soil test, types of soil test, test for soil, test of soil in civil engineering, soil test procedure for construction, soil test in civil engineering, soil testing, test of soil, pre-construction soil testing, types of soil test in civil engineering, types of soil testing, tests on soil, soil testing procedure for construction, tests on soil in civil engineering, soil testing parameters for construction, soil testing for building construction, soil test before construction, soil testing report for construction, soil testing methods in civil engineering, soil testing in civil engineering, soil tests for construction, soil test for building construction, different types of soil testing, soil test method, soil test civil engineering, soil test for house construction, how soil testing is done for construction
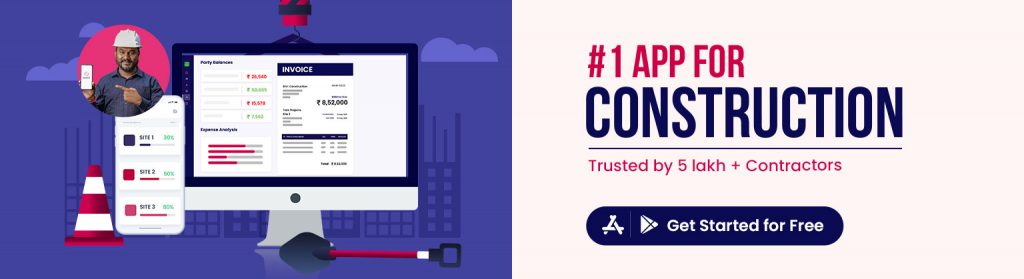