Work Hours
Monday to Friday: 7AM - 7PM
Weekend: 10AM - 5PM
Cut Material Waste with Digital Inventory Management System
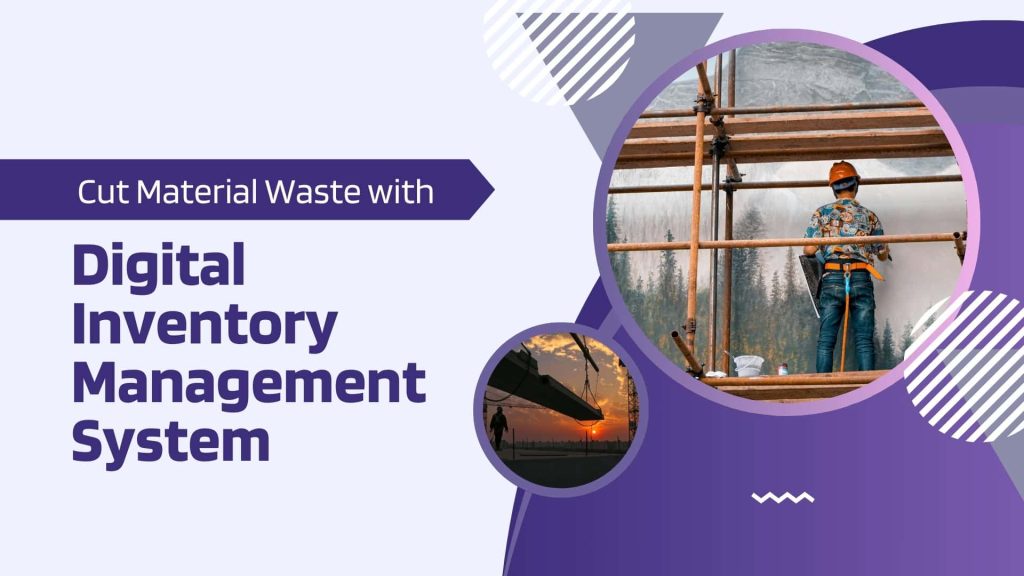
Knowingly or unknowingly, we often end up overordering material for our construction site. It is a common mistake which looks harmless but in reality, it’s one of the most silent profit-eaters in any construction business. Extra stock leads to wastage and increases storage costs. But Digital Tools can help you avoid over ordering and better inventory management system.
The Hidden Costs without Digital Inventory Management System
The mindset of over-ordering often easily comes but it leads to-
- Cash flow issue: Wasting on stock that might not be used in the same project again.
- Storage headaches: Over ordering can also cause problems of storage. With this problem, you will either pay for extra space or deal with clutter.
- Material wastage: Over ordering can also lead to material wastage especially for perishable material or project-specific items.
- Duplicate purchase: Often, with the lack of data or and lack of real-time visibility, can cause over ordering of material.
Biggest Problem? Manual Processes
Some methods are old and should be left behind like WhatsApp orders, Excel sheets, and paper records. With this method miscommunication is evident to happen, site engineers may not know what’s already in stock. Procurement teams may not be updated on what was just received. These problems lead to repeat orders which means unnecessary spending and over ordering. This is why digital tools are helpful. Let’s get to know how.
How Digital Tools Help You Take Control?
The chaos of manual tracking and lack of real-time update can be problematic. Digital tools eliminate these issues by offering centralized, transparent, and automated systems that bring clarity to your Inventory Management System.
- Monitor Usage as It Happens: With Digital Inventory Management System, every single entry is recorded which helps in giving visibility of stock. You no longer need to make assumptions or check physically, you can review stock levels anytime, anywhere. This helps in preventing guesswork and unnecessary orders.
- Prevent Double Orders: Digital tools bring coordination to the Inventory Management System. With transparency in material requests, material orders, and stock present at site, you can avoid ordering the same material twice. Everyone can get access to the same inventory data, removing confusion. Material approvals follow a structured workflow, which ensures accountability. This basically helps in fewer mistakes and accurate site requirements.
- Access Instant Reports and Insights: With data available in your digital tool, you can immediately generate reports and get to know how much of each material has been used over a time period and which sites are consuming more (or less) than expected. You can also get to know if there is any over-ordering at a site.
Best Digital Inventory Management System- Onsite
Onsite is specially made for construction sites. With this construction management software, a site supervisor can make a material request from the site, which is approved by a management team, which later on can lead to making material purchase. This material purchase will reach the site and you can also keep track of how much of it has been used. With this software, you can track how much of the material is being used everyday. If not used, you can also make an entry of material transfer to the other site. Every activity related to material can be tracked here. With our app, within three months, you can see a 20% drop in excess inventory. Teams will stop over-ordering because they could see what was already available. The savings will be immediate and impactful.
Conclusion
Digital Inventory Management System may not seem promising because it is hard to realize how much this section eats up your project cost. With Onsite, you can save time and money easily. Customers have saved up to 15% of their project cost just by using Onsite. So, if you are someone who is looking for an Inventory Management System and is planning to digitize your construction business then this article is for you.
Also Read: Increase Productivity with GPS Attendance Management System
FAQs
1. Why is over-ordering a problem in construction projects?
Over-ordering leads to excess stock that may never be used. It ties up your working capital, increases storage costs, and often results in material wastage- especially for perishable or project-specific items.
2. What causes over-ordering on construction sites?
The most common reasons include lack of real-time stock visibility, poor communication between site and procurement teams, manual record-keeping (like WhatsApp, paper, or Excel), and absence of approval workflows.
3. How can a digital inventory management system help reduce over-ordering?
Digital systems provide livestock data, centralized records, and approval-based workflows. They eliminate duplicate requests, enable smarter purchase planning, and ensure everyone- from site engineers to procurement- is on the same page.
4. What are the hidden costs of over-ordering?
Hidden costs include blocked cash flow, wastage from unused or expired materials, higher storage expenses, and operational delays due to clutter or mismanaged inventory.
5. Why are manual methods like Excel or WhatsApp not effective for inventory management?
Manual methods are prone to errors, miscommunication, and lack of real-time updates. These tools don’t provide structured tracking, approval systems, or analytics- leading to inefficiencies and repeat orders.